Alde Flash Butt Welding Machine For Band Saw
Alde Spot Welding Machines44 products
- Alde Flash Butt Welding Machine For Band Saw0 products
- Alde Flush Butt Welding Machines0 products
- Alde Multiple Piston Spot Welding Machines5 products
- Alde Pedal Type Spot Welding Machines6 products
- Alde Projection Type Spot Welding Machines20 products
- Alde Rezistance Butt Welding Machines7 products
- Alde Rezistance Seam Welding Machines4 products
- Alde Table Type Welding Machines2 products
Bald Mig Welding Machine5 products
Dess Copper Electrods10 products
Era Cooling System (Chiller)5 products
Esse Wire Bending Machine6 products
Ser Paintro & Nost1 product
Product categories
- Alde Spot Welding Machines 44
- Alde Flash Butt Welding Machine For Band Saw 0
- Alde Flush Butt Welding Machines 0
- Alde Multiple Piston Spot Welding Machines 5
- Alde Pedal Type Spot Welding Machines 6
- Alde Projection Type Spot Welding Machines 20
- Alde Rezistance Butt Welding Machines 7
- Alde Rezistance Seam Welding Machines 4
- Alde Table Type Welding Machines 2
- Bald Mig Welding Machine 5
- Dess Copper Electrods 10
- Era Cooling System (Chiller) 5
- Esse Wire Bending Machine 6
- Ser Paintro & Nost 1
No products were found matching your selection.
Butt and flash butt welding machines
Type DSS and EAS BALDESSERA butt and flash butt welding machines are designed for the efficient joining of saw bands, band knives and steel strip. Their strengths lie in precise, heavy-duty butt welding that can be reproduced in high quality. Emphasis was on the operator when designing the machine, with simple, ergonomic operation in mind.
The compact and robust design of the machine with its intuitive operation is aimed not only at industrial use in wood- and metal-processing operations, but also in mobile repairs. Used around the world, BALDESSERA DSS and EAS butt welding machines have been proving their quality and reliability on a day-to-day basis … and have been doing so for decades.
The benefits of our welding machines for saw bands, band knives and steel strip
• No addition of solder, flux or other additional materials
• Machine housings of a robust design for durability in a challenging production environment
• Perfectly aligned welds, free of offset by using highly accurate wear-free guides
•Uniform, high degree of distribution of pressure without the part slipping during the welding process by means of adjustable
manual, pneumatic or hydraulic clamping devices (varies
according to machine type)
• Quick-changing electrode inserts and pressure fittings for short
setup times
• Electronic components arranged in either machine housing or
separate cabinet for optimum protection against dirt and
damage
• Upset welding by means of an either mechanically or
pneumatically pre-tensed spring system for exactly the same
welding results
• Either sensitive or, as may apply, continuous adjustment of the
upset force and path for optimum welding results
• Automatic control of the welding process for precisely
repeatable welding results
• Precise multi-stage adjustment of the welding voltage for
optimum process parameters
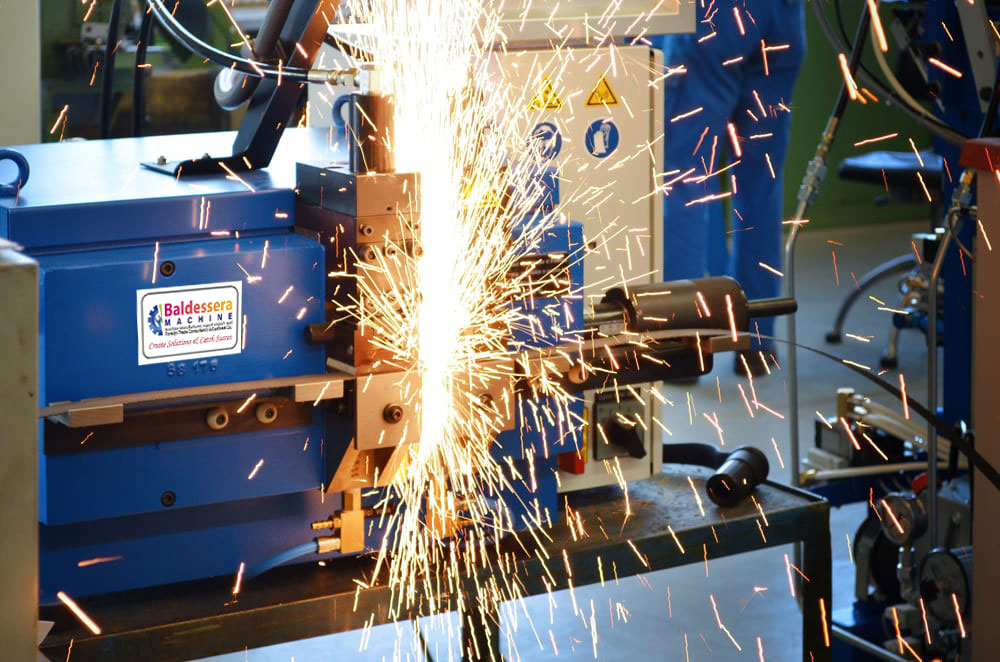