A water cooler chiller for a spot welding machine is essential for maintaining optimal operating temperatures during welding processes. These chillers help manage heat generated by the welding electrodes and the machine itself, preventing overheating and ensuring consistent performance.
1. **Cooling Capacity**: Chillers are rated based on their cooling capacity, typically measured in BTU or kilowatts, to match the heat load of the welding machine.
2. **Temperature Control**: Many chillers come with thermostatic controls to maintain a specific temperature range, ensuring efficient cooling.
3. **Flow Rate**: A suitable flow rate is crucial for effective cooling. Chillers should be capable of circulating water at a rate sufficient to keep the machine cool.
4. **Compact Design**: Many modern chillers are designed to be space-efficient, fitting easily into production environments.
5. **Durability**: Built to withstand industrial environments, these chillers are often made from corrosion-resistant materials.
Benefits
- **Extended Equipment Life**: By maintaining optimal temperatures, chillers help prolong the life of welding machines and components.
- **Improved Weld Quality**: Consistent cooling ensures stable temperatures, leading to better weld quality and consistency.
- **Reduced Downtime**: Effective cooling minimizes the risk of overheating, reducing the need for maintenance and downtime.
Applications
- **Manufacturing**: Used in various industries, including automotive and electronics, where spot welding is prevalent.
- **Heavy-Duty Welding**: Essential for high-volume or heavy-duty welding applications that generate significant heat.
Considerations for Selection
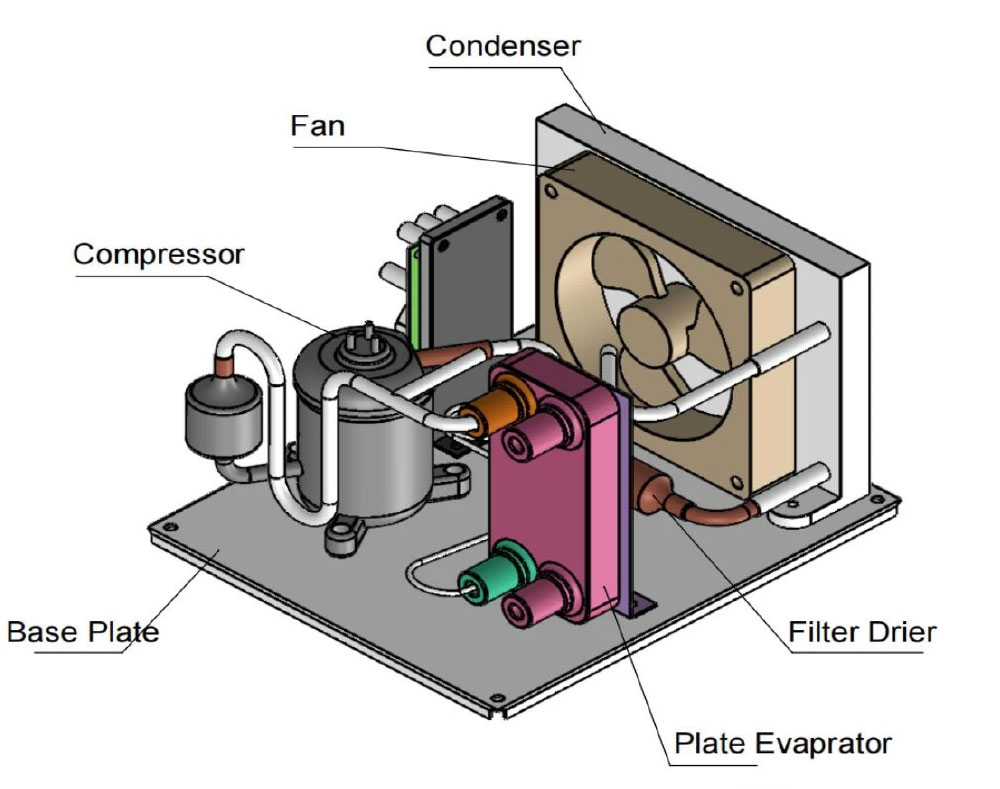
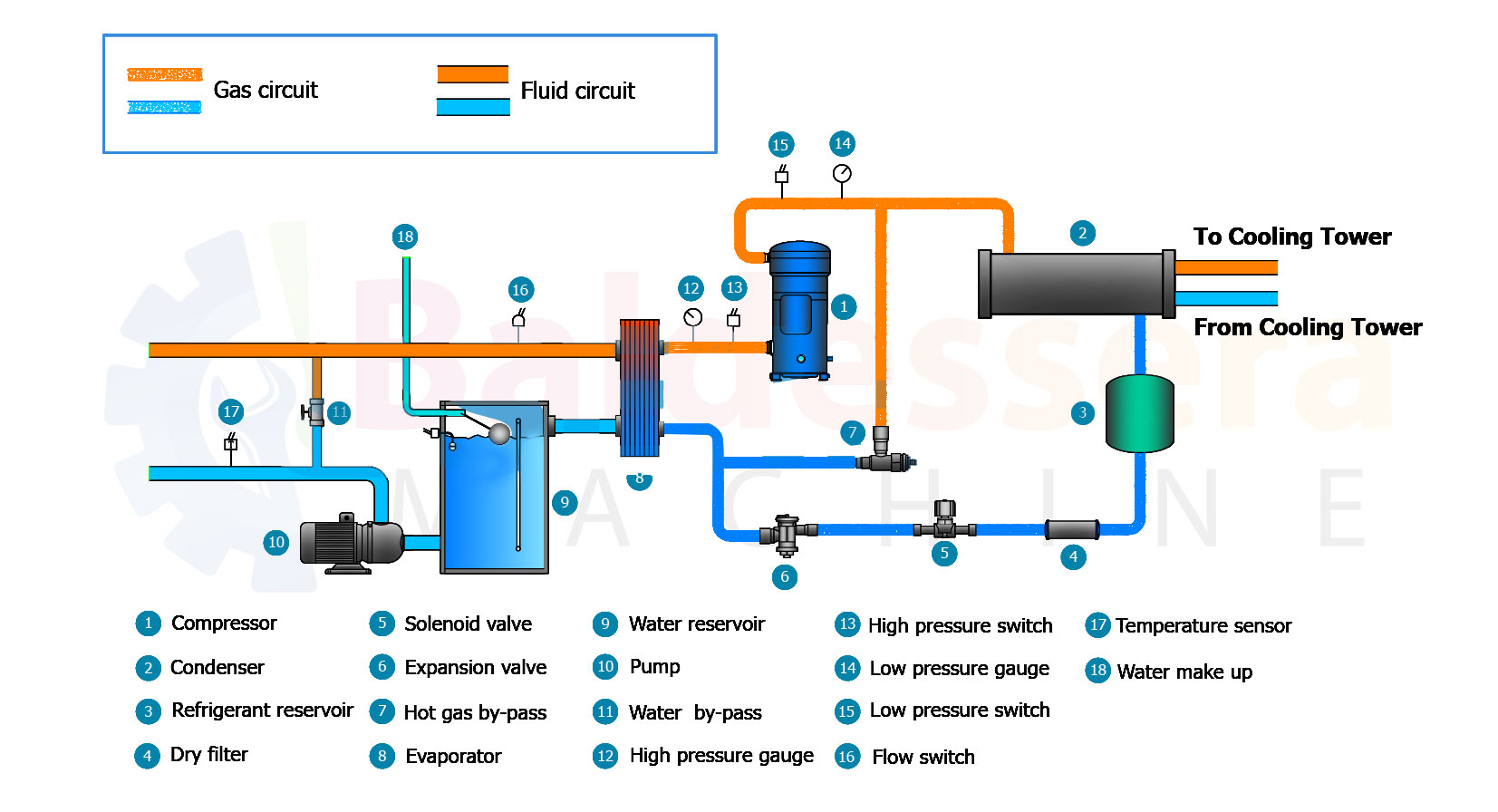