With the advancement of technology, Paintro replaces traditional air painting methods with nitrogen, which is smarter, more efficient, and environmentally friendly. As one of the pioneers of this transformation, Paintro is opening the doors to a new era in the paint industry. Our products, equipped with advanced technology, not only provide users with a faster, easier, and higher-quality painting experience but also minimize environmental impacts by enabling paint savings and contributing to a sustainable future. Committed to customer satisfaction and a solution-oriented approach, Paintro offers tailored solutions to meet the needs of its customers in every project. Take a step forward with Paintro and enhance your painting experience.
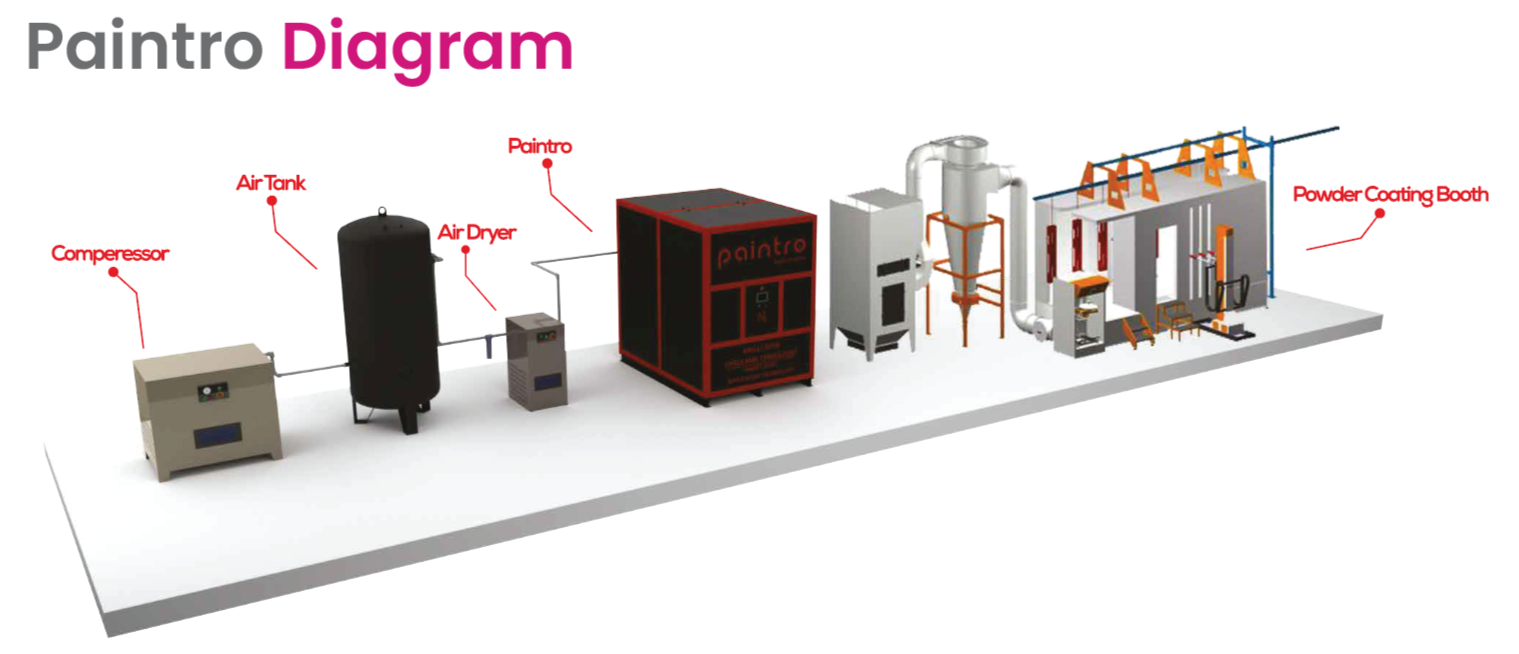
Why Paintro?
Paintro is an intelligent paint application technology designed to increase efficiency and quality in production while reducing costs by converting compressed air used in wet and powder paint lines into nitrogen gas. Nitrogen is a faster and finer gas compared to the ambient air, allowing paint particles to receive better charge, thus adhering more smoothly to the surface. With nitrogen, the initial adhesion ensures a more homogeneous spread of the powder film since there is no moisture or oxygen between the particles as they come together.
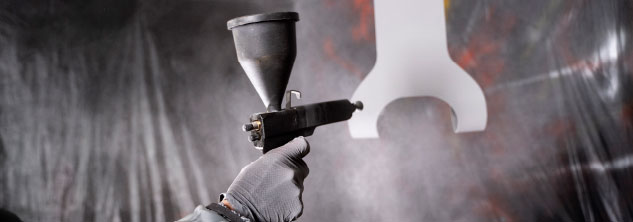
Smart Paint Application Technology
Using its selective permeability feature, Paintro separates nitrogen from compressed air to be used as a fluidizing carrier gas in all stages of powder paint application.
The system reduces the adhesion rate of the powder to the facility equipment. Nitrogen, the carrier gas in this system, is a clean gas and is perfect for applying powder coatings that tend to absorb contaminants like oils or moisture present in compressed air.
The gas produced by Paintro is an inert gas and does not contain substances that would cause contamination from the compressor. Therefore, application conditions are controllable and consistent in all seasons.
Paintro is mounted between the air compressor and the powder coating application system. This system works in conjunction with the user's existing equipment.
Paintro is suitable for Corona gun, Tribo gun, and wet paint gun systems.
Paintro enables faster color changes, material savings, a cleaner working environment, and reduced application time.
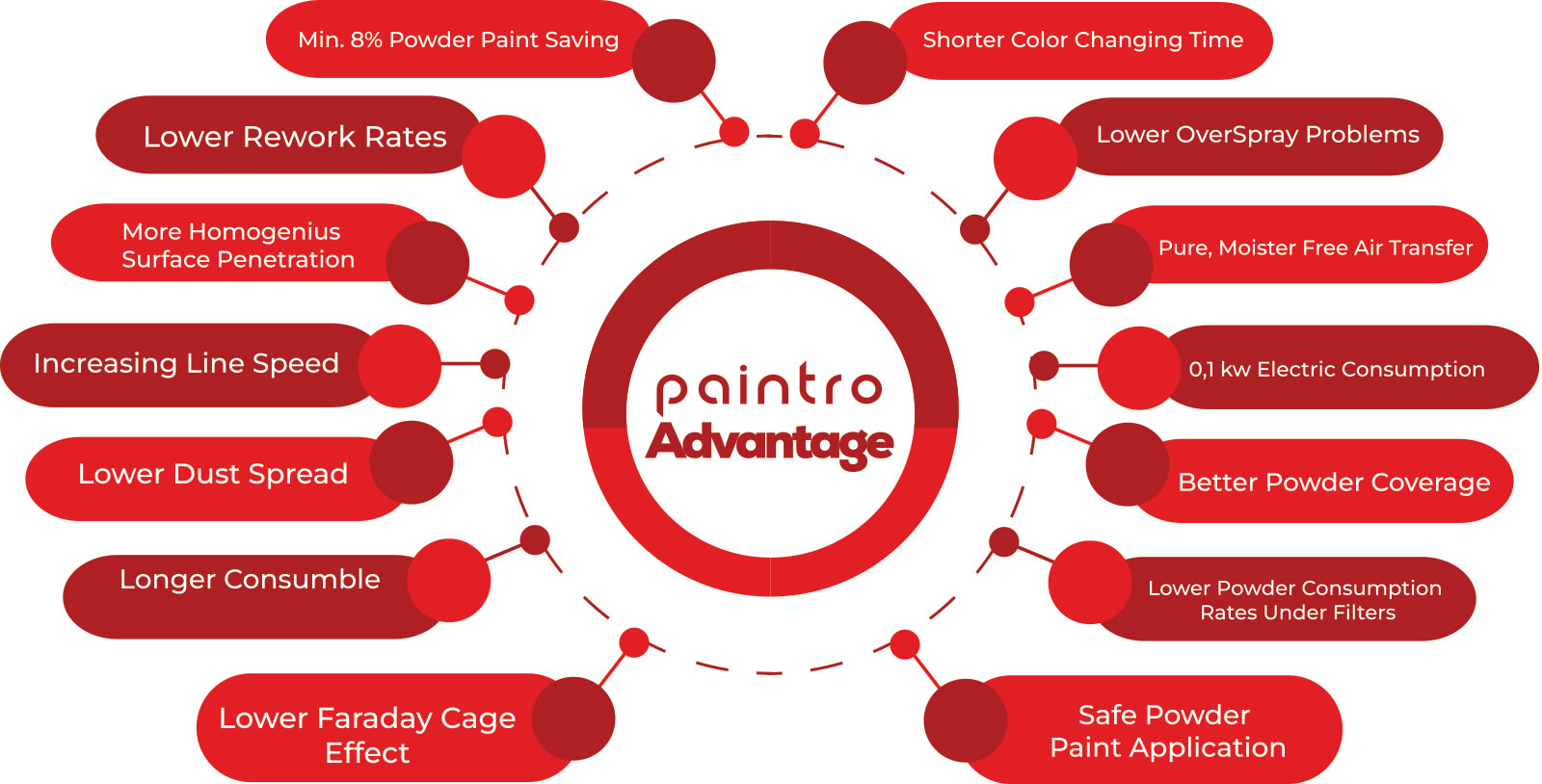
The Faraday Cage Effect
It enables easier application of thin parts by utilizing the characteristic properties of nitrogen.
Minimum 8% Paint Savings
With the Paintro paint application system, it reduces dusting, increases charging capability, and thanks to homogeneous paint spread, it provides up to 30% paint savings.
Dry Film Surface Appearance
Through improved homogeneous spreading and orange peel effect, a better surface appearance is achieved.
Advanced Control Of Electrostatic Charge With Paintro
Financial Gains
Guaranteed savings of 8% on total paint use
Increasing the transfer efficiency of powder coating
Optimization and ease of control of all application parameters
Minimizing waste paint generation
Environment and Safety
Improving working environment conditions with cleaner cabins
Better worker conditions duo to continuous and repeatable application conditions
Elimination of the possibility of static explosions
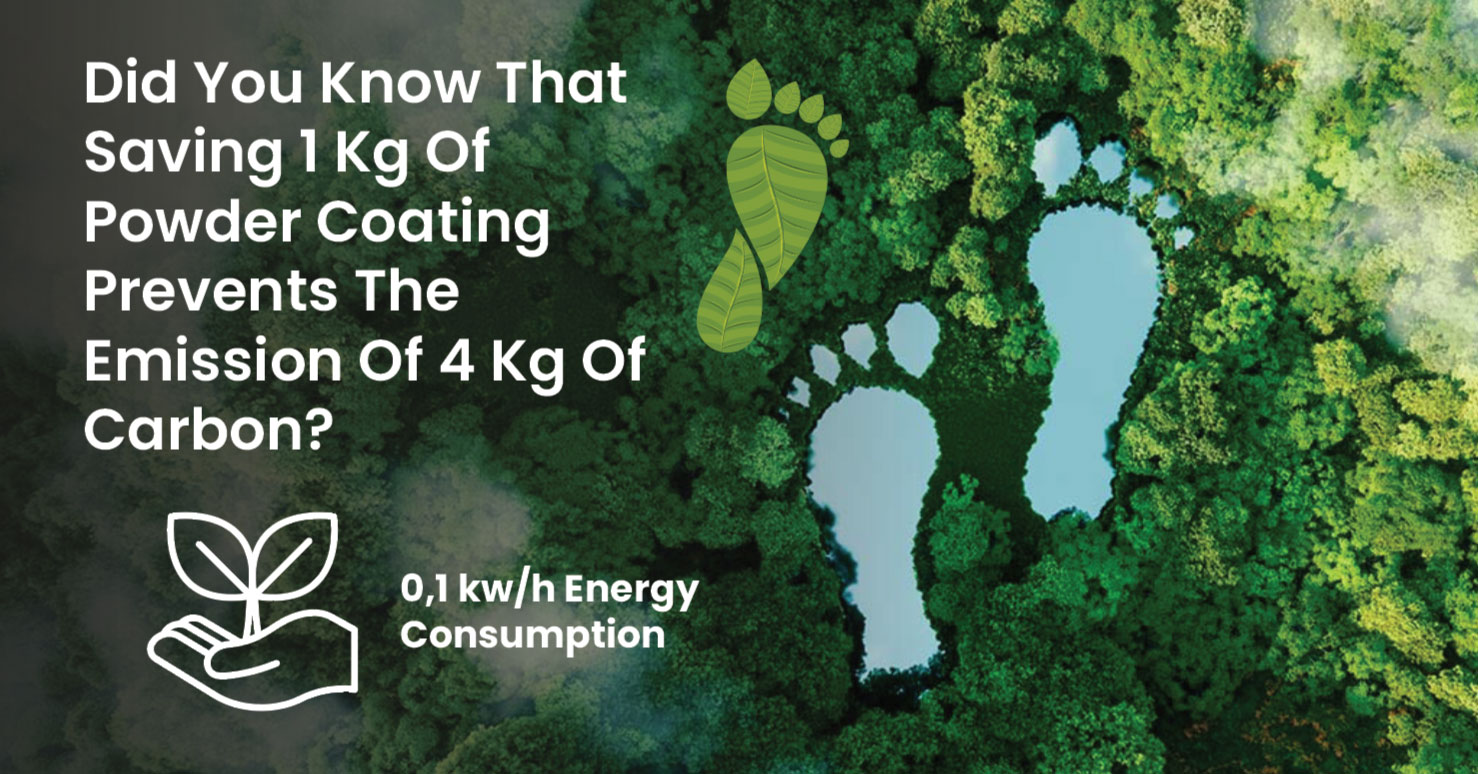
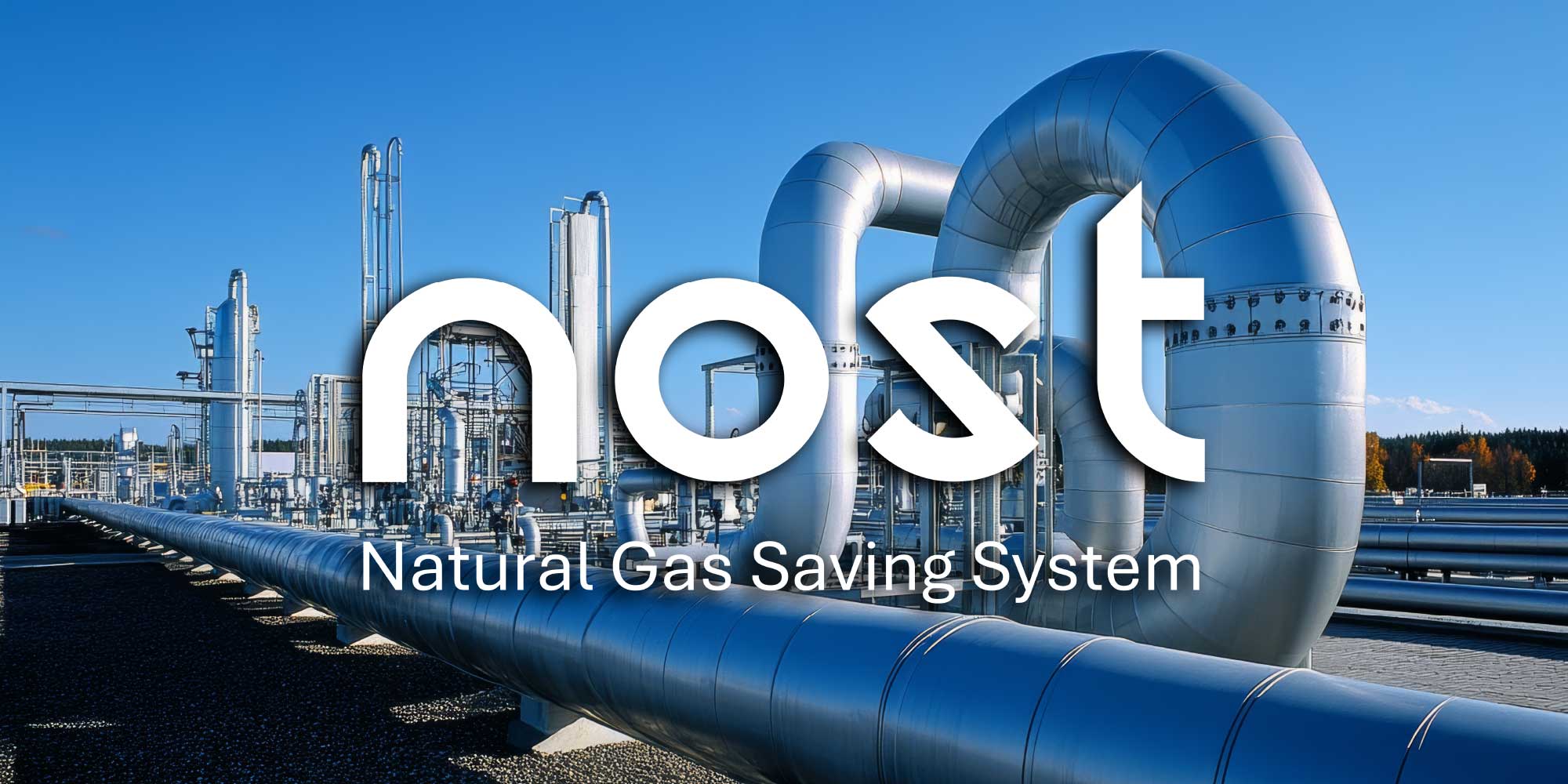
What Is Nost?
Nost is a 4-component system designed to save natural gas.
- Control unit that makes combustion efficiency more effective.
- It produces oxygen.
- Stores oxygen.
- It provides combustion controlled feeding.
How Does Nost Provide Saving?
Current systems; It is realized with the combination of air + natural gas. These systems carry out the combustion process by mixing flammable natural gas with the total air containing 21% combustible gas oxygen + 78% nitrogen + 0.9% argon and other gases.
Nost increases combustion efficiency by changing the mixing ratios in the current combustion process with the pure oxygen it produces.
The general working principle of Nost is based on increasing the amount of burning gas and ensuring better combustion of carbon in natural gas by supplementing pure oxygen. The increase in calorific value as a result of more heat being produced is a clear indicator of this result.
Ceramic Industry Working Details
Nost is mounted on a zone section of the ceramic oven with 4 burners, via external bypass. During the trials, the natural gas and air supply of this region was completely separated by bypass and controlled by Nost.
In test measurements, there is a meter on the natural gas line, an air flow meter on the Nost supply line, an electricity meter on the Nost electricity supply line, a pressure manometer on the natural gas line, a temperature manometer on the natural gas line, an air analyzer on the combustion air supply line, an analyzer that can measure the amounts of air and natural gas is installed on the burners. The system is measured in terms of both production and consumption.
Measurements were carried out after the oven was set to a certain temperature and was switched to automatic mode.
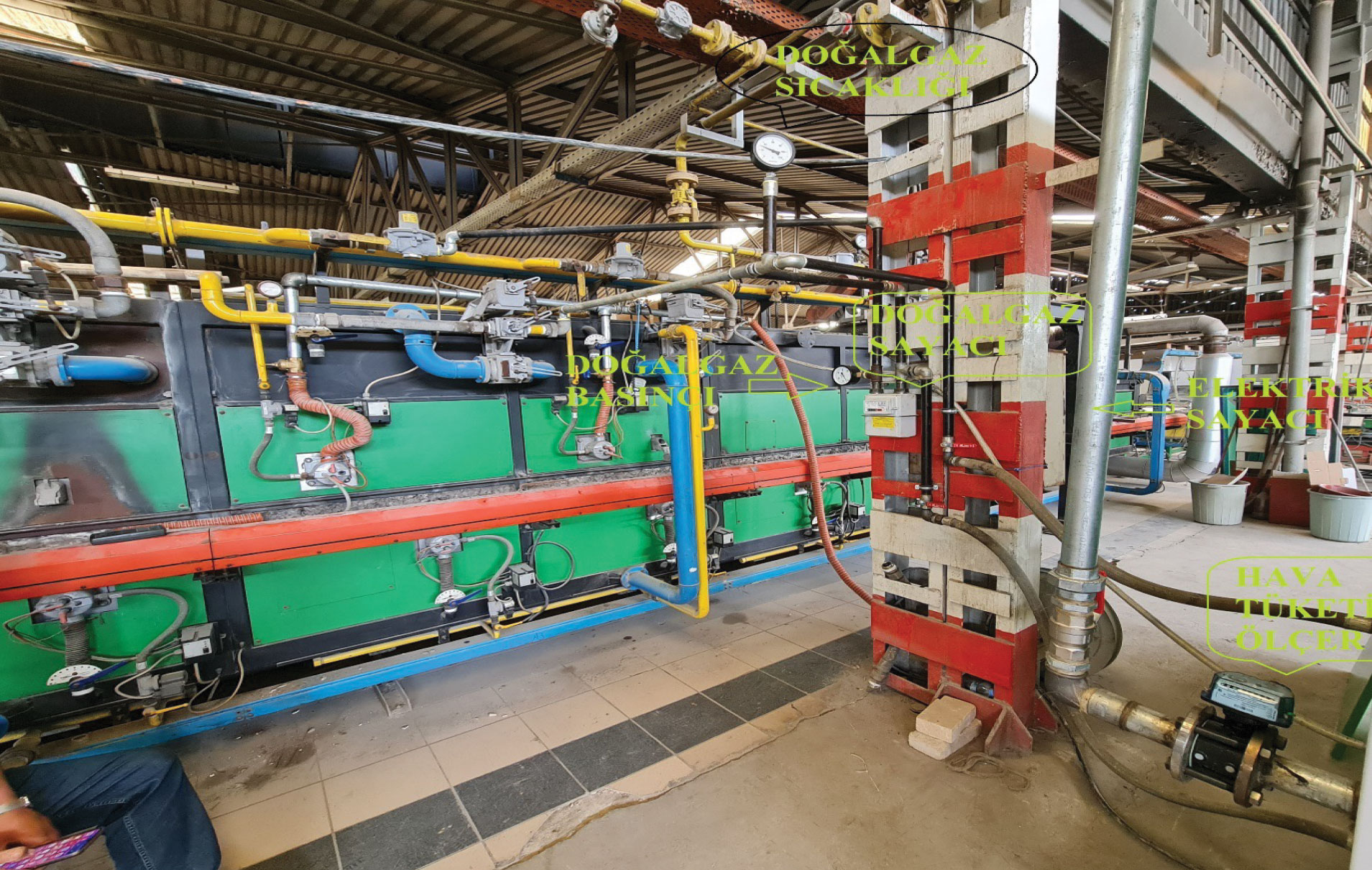
Mounting Method
Case Study 1
- In the test zone inside the oven (zone 2), 4 burners were operated for 4 hours with a constant gas supply. The 2nd zone probe measurement temperature was measured as maximum 248 C. No rise above this temperature was detected. (The current situation)
- The same zone with the same gas supply value was supplemented with Nost. Shortly after, the Max temperature was measured as 315 C.
Another observations between the two measurements were that with the support of Nost, the temperatures in the zones that were not actively working increased much more than their current situation. - While Nost was activated, the calorific value in constant gas supply was measured to be much higher than in the current system.
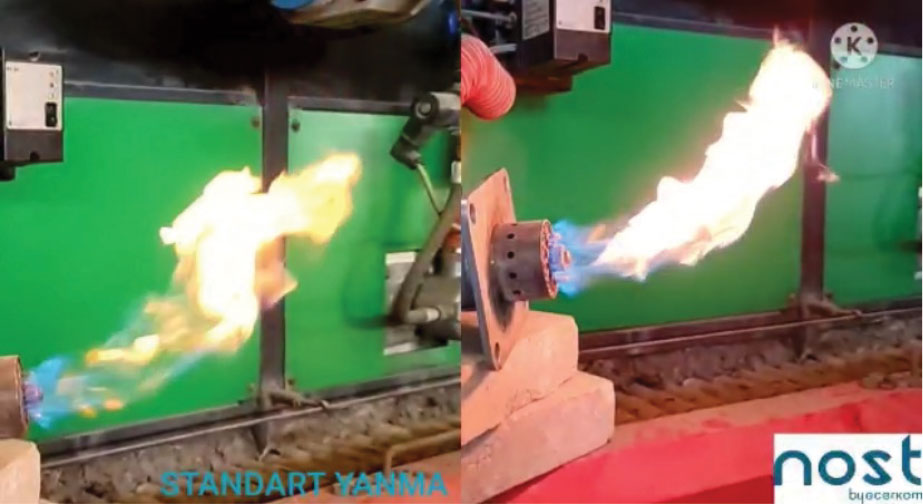
Nost and Current System Flame Display
Case Study 2
- In this trial, the oven set values were automatically fixed at 350 C.
- Measurements were carried out in the oven zone, which was set at 350 C and operated in automatic mode.
- These were the measurement results of the current and Nost experiments, where the gas and air temperatures are equivalent, especially at noon.
- In other regions outside the region where the measurements were made, the temperature increase was higher than the current situation when Nost was active.
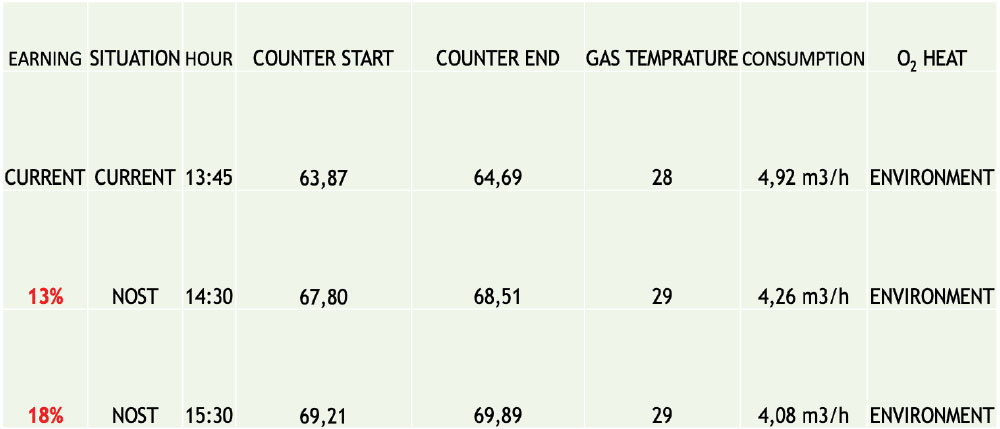
Case Study 2
- The ideal flame length and color for ceramic kilns were determined.
- As a result of the increasing calorific value, the project for frit furnaces became clear.
- It was stated that it was ideal for spray furnaces as a result of the increased calorific value.
- The amount of oxygen to be integrated into the system can be adjusted at any time.
- Savings of up to 25% in the size of the released flame were measured. (Fritt Oven Working principle).
- Maximum 5-7% of the savings obtained in the trials was calculated as the energy expense required for the operation of the Nost system. (Compressor air use etc.)